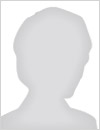
This will count as one of your downloads.
You will have access to both the presentation and article (if available).
Two of these channels are high resolution imagers (HRI) at respectively 17.1 nm (HRI-EUV) and 121.6 nm (HRI-Ly∝), each one composed of two off-axis aspherical mirrors. The third channel is a full sun imager (FSI) composed of one single off-axis aspherical mirror and working at 17.1 nm and 30.4 nm alternatively. This paper presents the optical alignment of each telescope.
The alignment process involved a set of Optical Ground Support Equipment (OGSE) such as theodolites, laser tracker, visible-light interferometer as well as a 3D Coordinates Measuring Machine (CMM).
The mirrors orientation have been measured with respect to reference alignment cubes using theodolites. Their positions with respect to reference pins on the instrument optical bench have been measured using the 3D CMM. The mirrors orientations and positions have been adjusted by shimming of the mirrors mount during the alignment process.
After this mechanical alignment, the quality of the wavefront has been checked by interferometric measurements, in an iterative process with the orientation and position adjustment to achieve the required image quality.
The HRI channel is based on a compact two mirrors off-axis design. The spectral selection is obtained by a multilayer coating deposited on the mirrors and by redundant Aluminum filters rejecting the visible and infrared light. The detector is a 2k x 2k array back-thinned silicon CMOS-APS with 10 μm pixel pitch, sensitive in the EUV wavelength range.
Due to the instrument compactness and the constraints on the optical design, the channel performance is very sensitive to the manufacturing, alignments and settling errors. A trade-off between two optical layouts was therefore performed to select the final optical design and to improve the mirror mounts. The effect of diffraction by the filter mesh support and by the mirror diffusion has been included in the overall error budget. Manufacturing of mirror and mounts has started and will result in thermo-mechanical validation on the EUI instrument structural and thermal model (STM).
Because of the limited channel entrance aperture and consequently the low input flux, the channel performance also relies on the detector EUV sensitivity, readout noise and dynamic range. Based on the characterization of a CMOS-APS back-side detector prototype, showing promising results, the EUI detector has been specified and is under development. These detectors will undergo a qualification program before being tested and integrated on the EUI instrument.
View contact details
No SPIE Account? Create one