|
ACCESS THE FULL ARTICLE
No SPIE Account? Create one
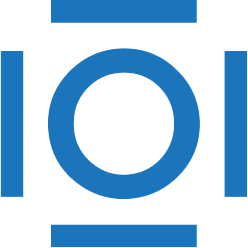
CITATIONS
Cited by 12 scholarly publications and 2 patents.
LIDAR
Sensors
Hough transforms
Safety
Clouds
3D image processing
Algorithm development