|
ACCESS THE FULL ARTICLE
No SPIE Account? Create one
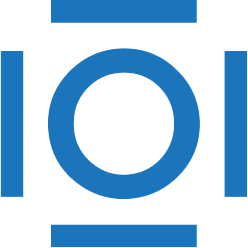
CITATIONS
Cited by 9 scholarly publications.
Sensors
Aluminum
Acoustic emission
Ferroelectric materials
Analog electronics
Data acquisition
Neurons