|
ACCESS THE FULL ARTICLE
No SPIE Account? Create one
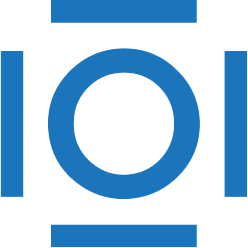
CITATIONS
Cited by 8 scholarly publications.
Etching
Silicon
Polymers
Manufacturing
Semiconducting wafers
Microelectromechanical systems
Bulk micromachining