This paper outlines some of the large mirror design methodology and understanding required to meet specified performance criteria for both monolithic lightweight and thin solid meniscus design approaches. These criteria are many. The optic must be shown capable of meeting performance goals during a changing gravity environment, for ground based telescopes, often looking from horizon to zenith, or be tested for the zero-g environment of space. It must further be insensitive to, or provide accommodation for, thermal swings about the nominal fabrication temperature. At temperature, it must preclude excessive error causes by real time thermal gradients. It must resist vibratory and wind loadings as well, and be of adequate strength to withstand all phases of handling and transportation in various stages of completion. The mirror must be generated, cut, ground, polished, tested, mounted, and coated. During these stages, the effects of residual stress, temperature, assembly tolerances, mount force errors, tool pressure, bimetallic distortion, surface flaws, and humidity must be duly considered to meet the stringent criteria of fractional visible wavelength performance and fractional arc second encircled energy requirements. The body of this paper presents an overview of the detailed analyses required to meet such criteria. Discussed are methods of supporting, mounting, and controlling such optics. The analytical tools of finite element math modeling are presented which assist in determining effects of material inhomogeneities, thermal strain, initial stress conditions, lightweighting, and mirror curvature, which play an important role as the diameter to thickness ratio increases. Material phenomenon and comparative trades are developed to aid in the choice of ideal candidates. Design examples from experience are finally given to illustrate the sensitivity of proven optics to the design criteria which have met stringent performance goals. These include lightweight monolithic optics with diameter to thickness ratios in excess of 15:1 and thin meniscus designs with ratios in excess of 100:1. In the latter case, active control is demanded, and correctability to both fabrication and operational errors is discussed, including actuator count determination. |
ACCESS THE FULL ARTICLE
No SPIE Account? Create one
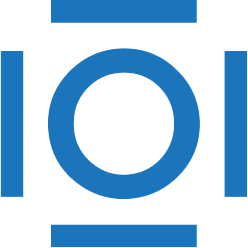
CITATIONS
Cited by 2 scholarly publications.
Mirrors
Optical mounts
Space telescopes
Assembly tolerances
Astronomical imaging
Optical fabrication
Polishing